Transmission Line Tower Item Specific
Product name | Transmission line tower |
Voltage grade | 10KV-500KV |
Raw Material | Q255B/Q355B/Q420B |
Surface treatment | Hot dip galvanized |
Galvanized thickness | average layer thickness 86um |
Painting | customized |
Bolts | 4.8;6.8;8.8 |
Certificate | GB/T19001-2016/ISO 9001:2015 |
Lifetime | More than 30 years |
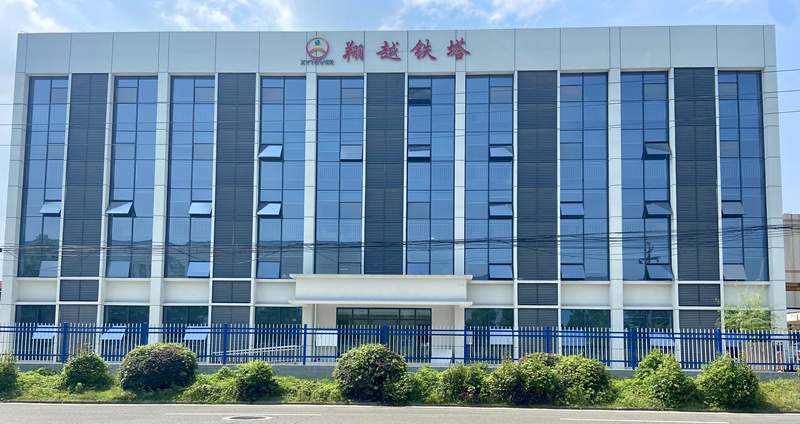
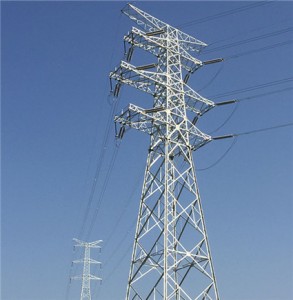
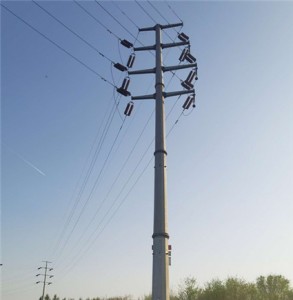
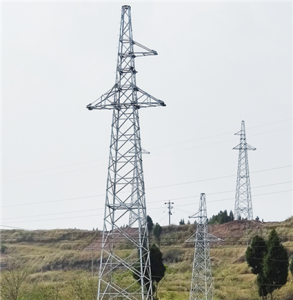
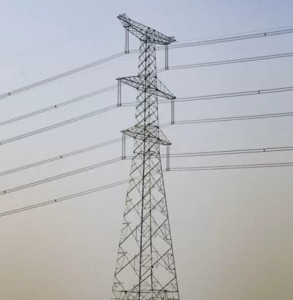
power transmission pole
single circuit lattice tower
double circuit lattice tower
What We Do
Products Classification
X.Y. Towers is a leading company of high voltage transmission line in south west China.Established in 2008,as a manufacture and consulting company in field of Electrical and Communication Engineering,it has been providing EPC solutions to the growing demands of Transmission and Distribution(T&D)sector in the region. Since 2008,X.Y towers has been involved in some of the largest and most complicated electrical construction projects in China. After 15 years of steady growth.we provide array of services within electrical construction industry which includes design and supply of electricity transmission and distribution and electrical substation.Standards
Manufacturing standard | GB/T2694-2018 |
Galvanizing standard | ISO1461 |
Raw material standards | GB/T700-2006, ISO630-1995, GB/T1591-2018;GB/T706-2016; |
Fastener standard | GB/T5782-2000. ISO4014-1999 |
Welding standard | AWS D1.1 |
EU standard | CE : EN10025 |
American Standard | ASTM A6-2014 |
Tower Assembly & Inspection
Hot-Dip Galvanization
Quality of Hot-dip galvanizing is one of our strength, Our CEO Mr. Lee is an expert in this field with reputation in Western-China. Our team has vast experience in HDG process and especially good at handling the tower in high corrosion areas.Galvanized standard: ISO:1461-2002.
Item | Thickness of zinc coating |
Standard and requirement | ≧86μm |
Strength of adhesion | Corrosion by CuSo4 |
Zinc coat not be stripped and raised by hammering | 4 times |
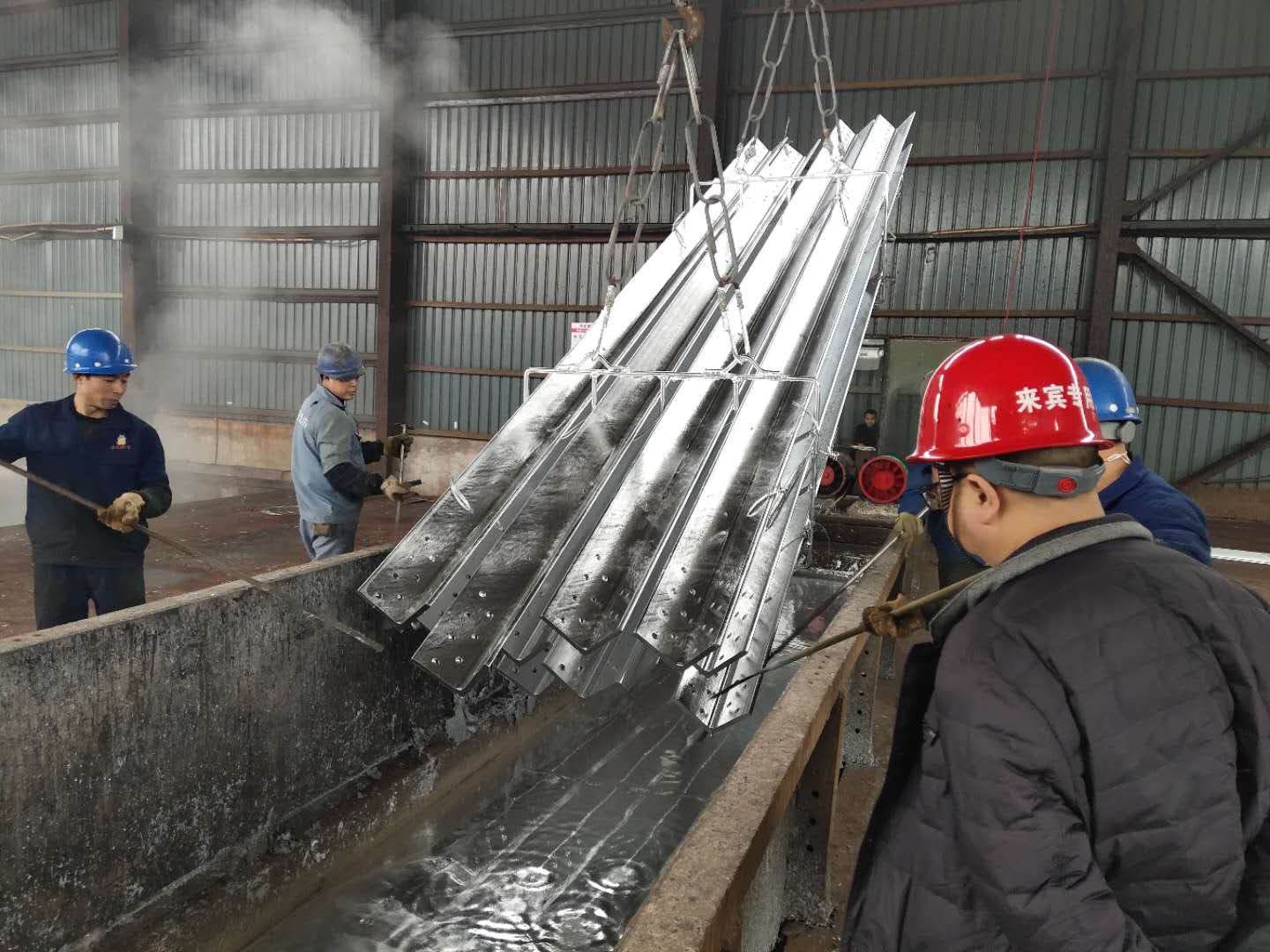
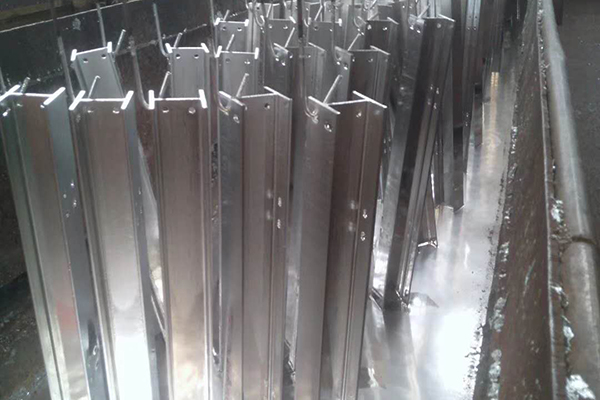
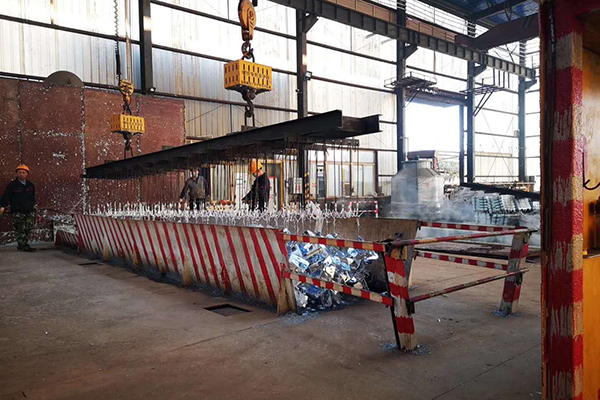
XYTower has a strict test protocol to ensure all products we fabricate is quality. The following process is applied in our production flow.
Sections and Plates 1. Chemical composition (Ladle Analysis) 2. Tensile Tests 3. Bend Tests Nuts and Bolts 1. Proof Load test 2. Ultimate Tensile Strength test 3. Ultimate tensile strength test under eccentric load 4. Cold bend test 5. Hardness test 6. Galvanizing test All the test data are recorded and will be reported to the management. If any flaws are found, the product will be repaired or scraped directly.
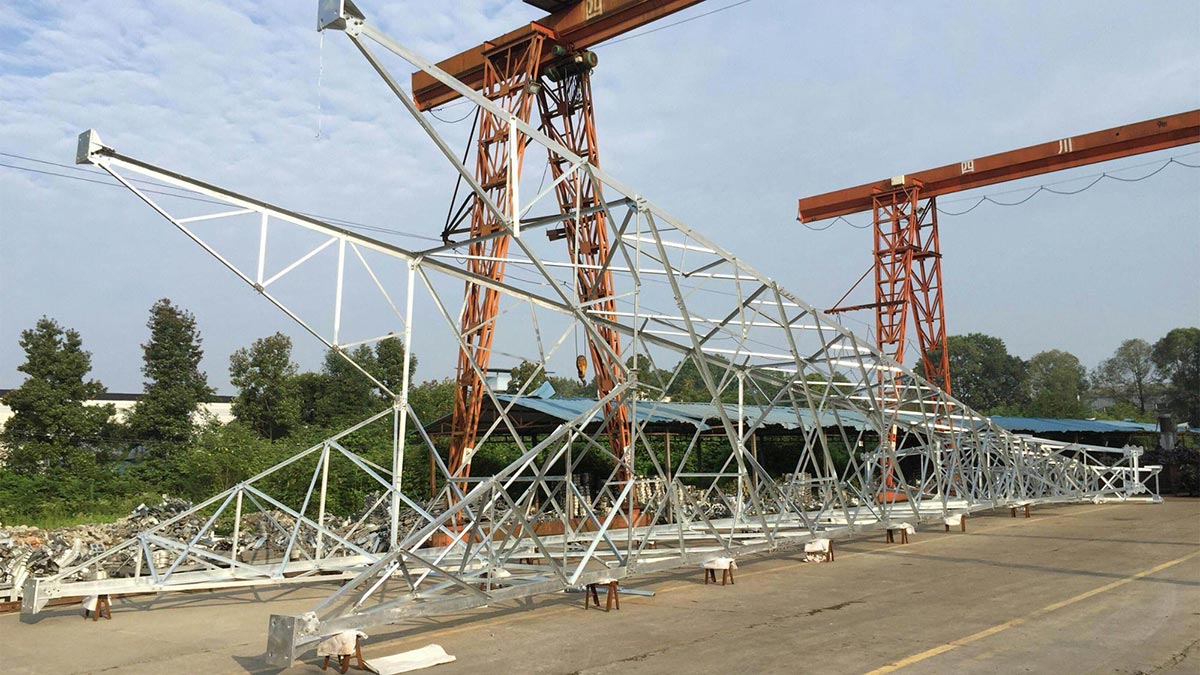